As the world’s top producer and consumer of lithium-ion batteries - and its rapidly growing recycling sector - China controls much of the global battery supply chain. It’s wielding that fact as a sword against the United States and its allies - perhaps not unfairly - as part of its retaliatory measures in the overarching battle for global dominance between the two superpowers.
While the U.S. bans Chinese battery making companies from doing business with American companies, the Middle Kingdom has realised the leverage it gains by using its monopoly over the production, refinement and manufacturing of key critical minerals - where they were cheaply outsourced by the West for decades.
Find out more: Export ban: China goes tit-for-tat with US in epic trade war
Move over Tesla?
The West - led by America post-WWII - could be perceived to have wielded advanced technological innovations to assert itself as the world's leader into the future.
If that is true, then perhaps China's own innovations in battery tech could be a catalyst to usher in the East as the world's next top dog in auto tech.
And if you keep reading, you'll see why it's near inevitable that China will likely (unless you're me and think it already is) become the next leader in energy and transport innovations.
China controls global battery market
…and we're not talking about breeding chickens. Say hello to the most globally significant automotive company on the planet, Chinese battery making behemoth: Contemporary Amperex Technology (HKEX : CATL).
CATL and rival compatriot BYD (which uses the formers' batteries for their EVs, mind you) combined account for 55% of the world's battery production - including EVs.
If you add the other four Chinese producers, the nation collectively controls a staggering 67.5% of the global market.
By contrast, South Korea's top three combined have shrunk from 23.2% of market share, down to 18.7% in just the last 12 months.
With over a third of global battery production itself, CATL's tentacles are global, leaving no sector that needs a battery without its influence.
More than a third of all new vehicles sold in China are now electric, far ahead of the second largest EV market globally (Europe), where only an eighth of new sales were EVs last year.
Meanwhile, analysts tip China will reach its EV target of 50% new sales by 2026 - a whopping 10 years ahead of schedule.
CATL's IPO success
Sanctions imposed in January by the U.S. government deemed the US$171 billion market-capped company's alleged Chinese military links a threat to national security.
Barred from Wall Street, CATL was undeterred, listing on the beleaguered Hong Kong Stock Exchange (HKEX) and banning onshore U.S. institutional investors from participating.
Yet despite no capital investment from America, a fever pitch grew around its recent initial public offering (IPO) and the battery giant raised US$4.7 billion at a below average 6.7% discount to VWAP for it to become the world's largest IPO so far this year.
First day of trade saw CATL's share price of HK$263 jump 16%, followed by a further 9% the day after.
The company's investments and spheres of influence spread right across the battery value chain - via ownership, operation, joint ventures or shareholding in a variety of critical minerals mines, processing facilities, transportation and end-product manufacturring.
Worldwide reach
I never thought I'd mutter, let alone write the first 20 words of this next sentence:
The Chinese vehicle innovator has a 51% controlling stake in Geely - a standalone brand and owner of once-Swedish carmaker Volvo (acquired in 2010) - along with another 14 car brands including ZEEKR, Polestar and Lotus under its umbrella.
It takes no stretch of the imagination to assume the company supplies them all with CATL EV batteries and associated parts.
It sells those very same batteries to rival carmakers too, including Tesla - which has a running supply agreement with the battery giant until December this year - and other globally recognised brands such as Volkswagen, Ford, Toyota, Stellantis, BMW and Mercedes-Benz.
CATL's run
2011 - CATL founded in Ningde, China by Robin Zeng (former ATL/TDK executive)
2017 - Shipped 12GWh of batteries across the globe to become the world's largest EV battery shipper
2019 - Bought 4.9% of Aussie lithium miner Pilbara Minerals (ASX : PLS) at 30c/shin 2019, sold for $4.10/sh in 2023 - netting a cool A$555 million
2018 - Announced/started 14GWh factory in Arnstadt, Germany in partnership with BMW - CATL’s first European plant
2020-21 - Expanded Chinese capacity, surpassing 70GWh global output; began solid-state battery R&D
2022 - Announced €7.3B investment in a 100GWh battery plant in Debrecen, Hungary
2022 - Began production at Thuringia, Germany plant; launched Shenxing battery line
2023 - Introduced the "Naxtra" sodium-ion battery brand; mass production planned for late 2025
2024 - Formed 50GWh joint venture with Stellantis…
Rivals
The EU-US car manufacturing conglomerate Stellantis, which commands a long list of brands - including Maserati, Dodge, Citroen, Peugeot, Alfa Romeo, Jeep, Fiat and more, is setting up in Spain of all places.
The Iberians haven't really been known as a hub of raw material production and manufacturing for about three decades, having started their decline in the 1990s.
Stellantis also resumed a 20GWh JV with Ford in Michigan and is focusing on securing its own slice of the new supply chains penning lithium offtake agreements with resources companies such as Vulcan Energy Resources.
In April 2024, Vulcan began producing lithium chloride in Germany, and plans to process it into battery-grade lithium hydroxide using direct lithium extraction tech to produce 24,000 tonnes per annum - enough to power ~500,000 EVs.
2025 – Completed Hong Kong IPO in May, raising almost $4.7 billion; shares jumped 16% on the first day; secured government guarantee for its 100GWh Hungary plant (construction planned for 2026).
…and the recycling too?
You betcha bottom yuan.
China, led by CATL, also resoundingly dominates the recycling of batteries, processing 3.6 million tonnes (Mt) per annum of scrap to make 2.5Mtpa worth of chemicals to be used for energy storage devices and systems.
They were accutely aware of their overreliance on importing the raw materials they couldn't produce from places like Australia decades ago.
According to Benchmark Intelligence’s latest recycling forecast, China's recycling output translates to 78% of global battery pre-treatment capacity and an eye-whopping 89% of black mass refining capacity.
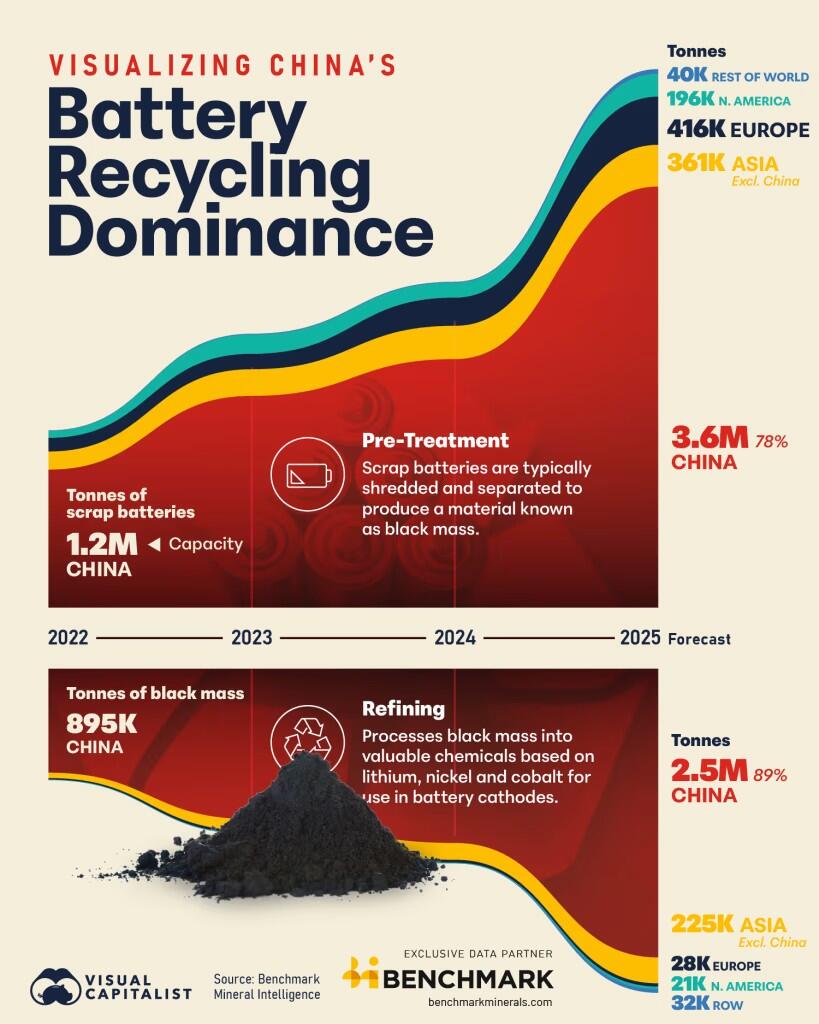
How are batteries recycled anyway?
The recycling process begins by collecting scrap from battery manufacturing plants and/or end-of-life batteries; and since China has the biggest EV market, its recycling industry has a major advantage in securing large amounts of feedstock.
Collected scrap then undergoes pre-treatment (usually involving mechanical shredding) to produce ‘black mass’ - a mixture containing lithium, nickel, cobalt, and other high-value battery metals.
While many regions outside the Middle Kingdom have focused on building pre-treatment facilities (for example, 28 out of the EU's 38 recycling plants only handle this stage of the process), both China and South Korea have developed extensive refining capacities.
The final step involves refining black mass into chemicals for new battery cathode materials. Some processors convert it directly into pre-cathode active material (pCAM), while others produce intermediate chemicals that require additional refining before being used in cathode production.
Due to their large refining overcapacity, the two nations must import black mass from regions such as North America, Europe and Australia, which, on the other hand, are undercapacity in their ability to refine.
Charging into the future with salt
In its quest to remain at the forefront of EV innovation, CATL last month revealed its Naxtra battery - the world's first mass-produced sodium-ion (regular 'ol salt) battery that's lighter, cheaper, faster-charging, more cold-resistant and longer-ranged than today's lithium-ion batteries.
If sodium-based batteries commercialise at scale, CATL looks best positioned to make it happen.
The company's global reach consists of 13 manufacturing plants and six R&D centres run by a 100,000+ workforce and is developing energy storage systems for both EVs and grid solutions.
Takeaway
It's a wake up call for America and the West, which clearly needs to accelerate deep R&D, material science, cell design and ecosystem innovation at a pace and ambition that matches or even exceeds China's just to stay relevant.